TABLE OF CONTENTS
New Feature: Being Stocked at the Warehouse and Order Updates
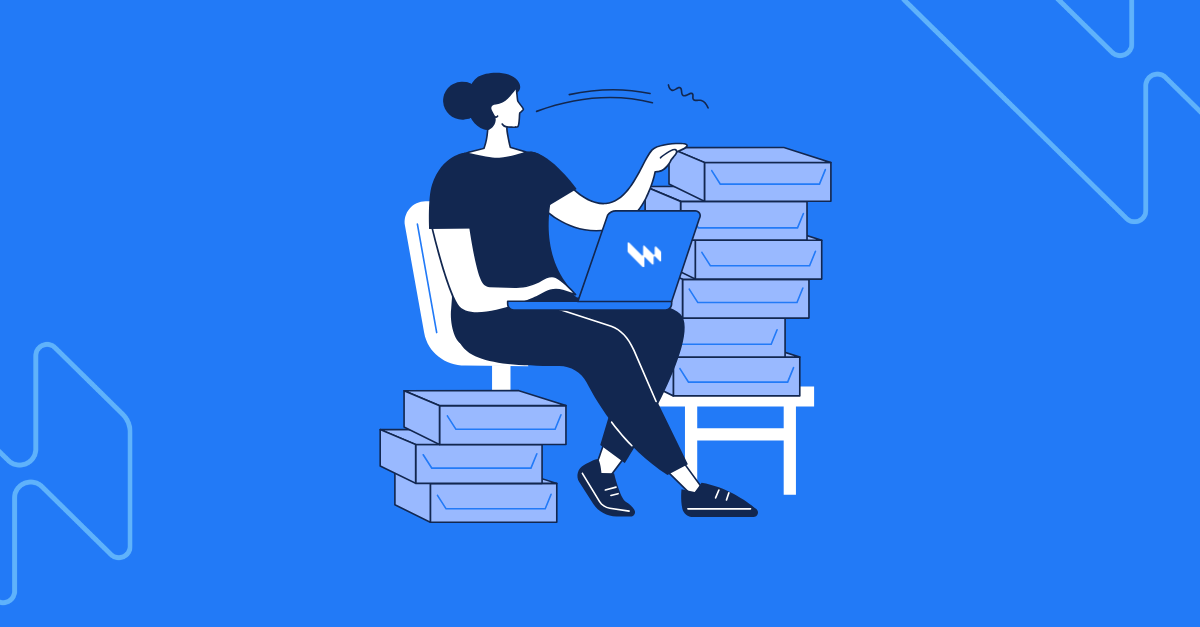
We’re excited to announce a powerful new automation for Workwize users—designed to streamline the management of your asset workflows. With this update, status updates for offboarding and order processes will happen automatically, making your logistics smoother.
What’s New?
Here’s what this feature brings to your Workwize experience:
-
Automatic Status Updates: Real-time updates for assets in offboarding (Offboard to Warehouse) and order fulfillment (Order to Warehouse).
-
New Intermediate Status: The dedicated status "Being stocked at the warehouse" indicates items that have arrived but are still being processed.
-
Proactive Issue Resolution: Automatically flags problems and generates actionable tickets for quick resolutions.
How It Works
Step 1: Automatic Transition to “Being Stocked at Warehouse”
-
When an item arrives at the warehouse, Workwize automatically updates its status to Being stocked at the warehouse.
-
This status reflects that the item has been delivered but is awaiting full integration into your inventory system.
Step 2: Finalizing the Delivery
-
Once the warehouse completes processing, Workwize updates the item’s status to Delivered, indicating it is ready for its next lifecycle stage.
-
If any issues are detected during processing (e.g., hold codes or missing items), Workwize flags these items and automatically generates a ticket for resolution.
Why It Matters
-
Save Time: Automating status updates reduces manual effort, letting your team focus on higher-priority tasks.
-
Enhanced Transparency: Clear differentiation between delivered and processed items removes ambiguity and provides a better overview of asset logistics.
-
Streamlined Issue Resolution: Proactive problem detection and ticket creation ensure delays and issues are addressed promptly.
Addressing Common Challenges
Many users have faced confusion when items show as "Delivered" in tracking systems but still require internal warehouse processing.
This is especially common for offboarding workflows and new orders.
The introduction of the Being stocked at warehouse status bridges this gap, providing a more accurate representation of the asset’s journey.
Technical Highlights
New Statuses
-
Offboarding workflows: New status - Being stocked at the warehouse.
-
Order fulfillment: New shipment status - Being stocked at the warehouse.
Automation Logic
-
When an item reaches the warehouse and is marked as delivered, Workwize transitions to Being stocked at the warehouse.
-
Once warehouse processing is complete, the status updates to Delivered, provided no issues are detected.
Exception Handling
-
Error Management: When issues arise, such as missing items or hold codes, Workwize generates a ticket with detailed information for swift resolution.
-
Notifications: Alerts and logs ensure complete status transitions and issue-tracking transparency.
Why This Matters to You
This feature is part of our ongoing mission to make asset management intuitive, automated, and efficient. By introducing intermediate statuses and automating key updates, we aim to simplify your workflows while providing a clearer view of your asset’s lifecycle.
IT teams use Workwize to manage their entire lifecycle of global IT hardware.
Recent articles
Stock up on IT equipment at local warehouses & other new exciting Workwize features
At Workwize, we're always looking for innovative ways to streamline the equipment onboarding...
Workwize Auto-Offboarding: Zero-Touch Asset Management for Departing Employees
Modern organizations face challenges managing employee transitions.
New Workwize Feature: Visibility on Second-hand IT equipment
For organizations that use Workwize, managing IT assets just got even simpler!
Ready to optimize your remote on- and offboardings?
Let’s schedule a short chat and see how we can help!